

METALS & MINERALS
Most facilities include multiple unit operations to enrich and refine the valuable materials and then treat the tailings before disposal. Many common fundamental mass transport and separations technologies are incorporated, some chemical and some physical in nature (size reduction, floatation, magnetic separation, roasting, leaching, selective precipitation, ion exchange, solvent extraction). In addition to the core process, utilities optimization and well-engineered stream recycling can often make the difference between a profitable or unprofitable facility.
We design the process from the fundamentals up and utilize the expertise of our client and specialized equipment manufacturers as needed to help ensure the process we design will perform at an optimum level.
AT PROCESS, WE HAVE THE EXPERTISE TO SUPPORT OUR CLIENTS IN DEVELOPING INNOVATIVE METALLURGICAL PROCESSES FROM A CONCEPTUAL THEORETICAL PROCESS, THROUGH BENCH SCALE AND PILOT PLANT TESTING, TO THE ENGINEERING, CONSTRUCTION AND START-UP PHASES OF THE FACILITIES.
Process Design Definition
Definition of the overall process system and technical requirements, predicting expected process behavior through modeling and simulation, as well as evaluating viable process alternatives. The process design provides a road map / blueprint for other design disciplines to follow.
-
Strategic planning support
-
Test work planning and follow-up
-
Design Criteria development
-
Feasibility /alternatives studies
-
Block Flow Diagrams (BFDs)
-
Conceptual design
-
Capital Project Development Support (FEL-0, 1, 2, 3)
-
Process simulation and analysis (METSIM, CHEMCAD, ASPEN, HYSYS)
-
Material and Energy balances
-
Process Flow Diagrams (PFDs)
-
Piping and Instrumentation Diagrams (P&IDs)
-
Process Equipment Specification
-
Permitting support
Rare Earths Element, Platinoids and Uranium Technology metals are elements used in advanced technological applications such as electronics, advanced technology systems, alternative energy sources and energy storage. Most of the applications for technology metals are recent and extraction processes are typically tailored to the specific mineral deposit structure. PROCESS’ design experts can assist with developing unique processes for your specific deposit using state-of-the-art physical and hydrometallurgical processes.


Process Design
“So, how many methyl-ethyl-wonderchemicalate plants have you designed anyway? We need Subject Matter Experts (SMEs) to design this process.”
Man, have we heard that before. No doubt, if you can find a whole design team of SMEs, that is normally a good way to go. But if methyl-ethyl-wonderchemicalate plants are hot, good luck getting that firm that has designed them all. If they are cold, that company won’t likely exist any more or never did. And there is one more thing…. We recently visited a specialty chemical plant that had hired an engineering firm that had designed (what they thought) was the exact same process before. Unfortunately they failed to take into account a small raw material change – and the new plant does not work. So SMEs are not always the best way to go.
Instead of looking for SMEs, why not hire some PDEs (Process Design Experts)? We have designed hundreds of processes, and for the majority of these designs, we were looking at chemistry that was new to us. As PDEs, we have learned a number of things that allow us to effectively design a process without having to have years of experience with the specific process chemistry. Some of these include:
-
Literature/internet research
-
Bench-scale and/or pilot plant data analysis
-
Experience with similar processes and/or chemistry
-
Plant floor experience
-
Using client SMEs
-
Detailed process design basis development
Process Design Experts (Continued)
-
Raw material specifications
-
All other operating goals and constraints desired by the plant owners/operators/engineers


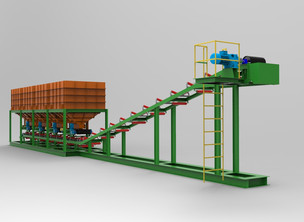

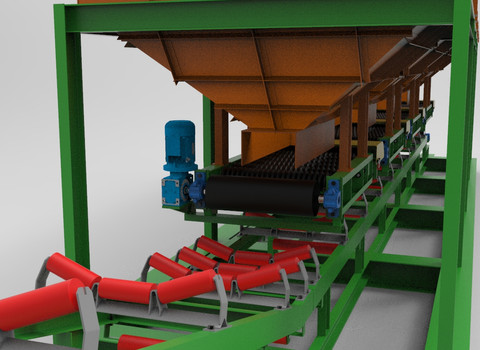







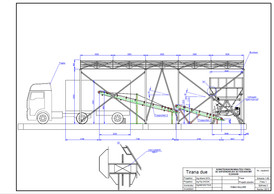




